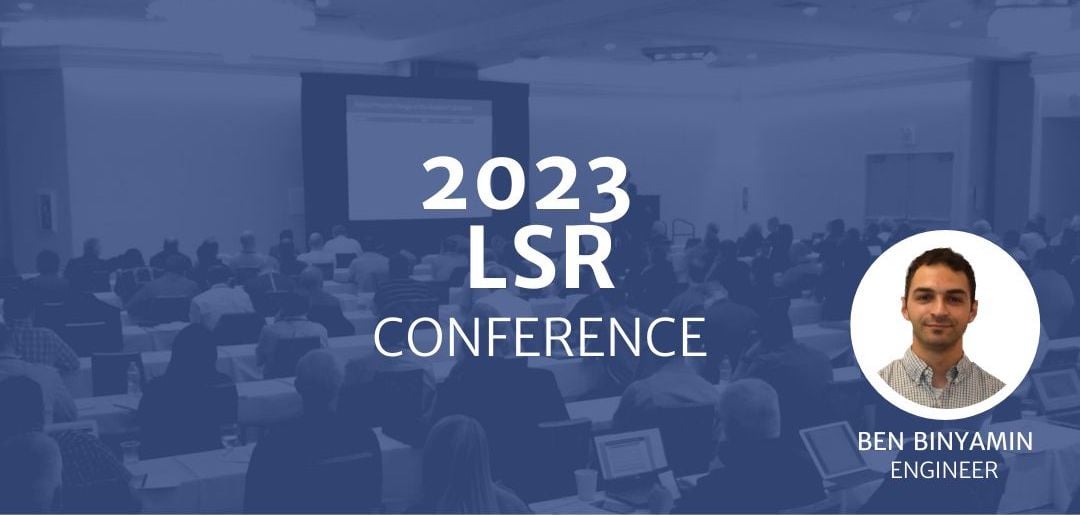
Last month, the industry came together for its annual Liquid Silicone Rubber (LSR) conference—a gathering of professionals from various segments to discuss the latest advancements and developments in our field. We were thrilled to have one of our skilled engineers, Ben Binyamin, represent us at this event.
During the conference, Ben gained invaluable insights from the diverse perspectives that LSR 2023 had to offer. His learnings weren't just confined to fellow CPG injection molders; they extended to medical molders, molding simulators, machine manufacturers, component designers, raw material manufacturers, pigment companies, and chemistry researchers.
His biggest takeaway was how the industry was reacting to the ever-changing global economy. Various industries and cultures alike seem to be dealing with similar challenges due to this unique economic situation. And seeing competitors come together to share insights was encouraging.
That’s why we were glad that Ben was able to present his own findings in his presentation, “CTQ Considerations in LSR Overmolding.” He discussed effective ways to analyze and prevent overmolding defects. This included how to identify problematic inserts/substrates that affect Critical To Quality factors, in order to prevent major issues in advance.
In case you missed it, here are the factors that can seriously hinder the overmolding process in certain situations:
- Inserts/substrates not properly molded.
- Parts contaminated by external sources.
- Substrate inconsistencies driven by process changes and/or raw material variations from suppliers.
- Substrates not properly prepared for the overmolding process.
Ben also outlined a process that, though more complex and time-intensive, has consistently improved our quality and better satisfied our customer needs. Here are the key steps he highlighted:
- Process to achieve a more repeatable product and focusing on limiting part-to-part variation.
- Create proper storage procedures to limit contamination.
- Have close communication with the customer to identify what the customer deems as an acceptable product.
- Be vigilant on the manufacturing floor to ensure proper training and attention to detail.
- Collaboration between Production and Quality to stop any problems or issues that arise.
Ben's presentation not only emphasized our commitment to quality, but also delved into how we, as an industry, can work thoughtfully with our customers to meet their needs efficiently and effectively, thus ensuring their satisfaction in a timely manner.
Overall, we were grateful our team made it to LSR 2023 and had the opportunity to educate our peers on some of our latest findings. At Extreme Molding, we are continuously looking for ways to foster growth, expand our knowledge, and we can’t wait to learn more at next year’s conference.
In the meantime, if you are looking for help with manufacturing your product, please contact us. We’d be happy to help.